Compressed air filter play a vital role in maintaining the quality of compressed air systems. However, like any mechanical component, they can encounter issues over time. In 2024, understanding these common problems and knowing how to address them can help ensure your systems operate smoothly and efficiently. Let’s explore the typical issues with compressed air filters and their solutions.
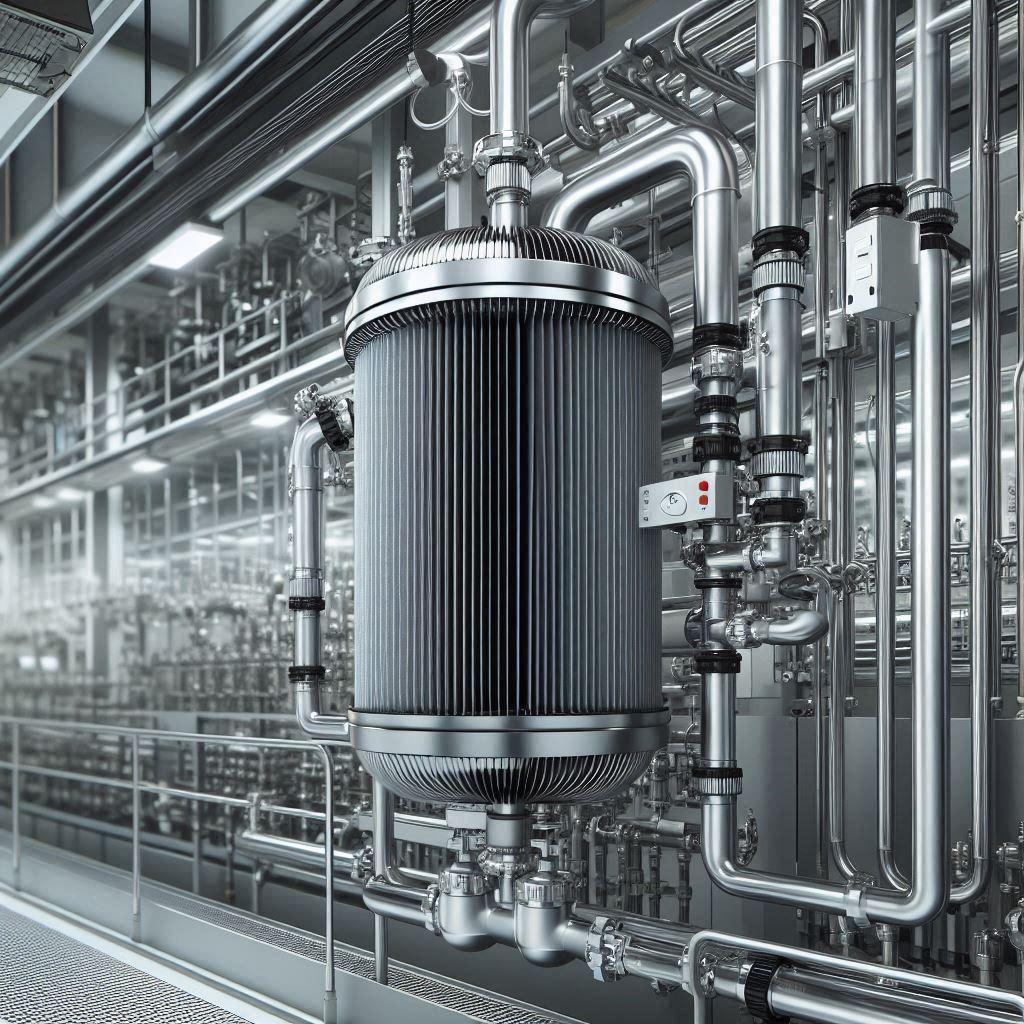
1. Clogged Filters
Problem Overview
One of the most common issues with compressed air filters is clogging. Over time, filters accumulate dust, dirt, moisture, and other contaminants, which can restrict airflow and reduce the efficiency of your system.
Symptoms
- Reduced airflow and pressure
- Increased energy consumption
- Unusual sounds from the compressor
Solution
Regularly inspect and replace filters as needed. A good practice is to check filters monthly, especially in dusty environments or where air quality is poor. Keep a maintenance log to track replacements and inspections. If you notice frequent clogging, consider upgrading to a higher-capacity filter or adding pre-filters to capture larger particles before they reach the main filter.
2. Moisture Buildup
Problem Overview
Moisture can accumulate in compressed air systems, particularly if the air intake is humid or if there are insufficient drying mechanisms in place. This moisture can cause corrosion, rust, and contamination.
Symptoms
- Water droplets in the air lines
- Decreased efficiency of tools and machinery
- Rust or corrosion on equipment
Solution
To combat moisture buildup, install a refrigerated or desiccant dryer downstream of your compressor. Regularly drain moisture from filters and separators. Schedule routine maintenance to check for leaks in the system that might allow moisture to enter.
3. Oil Contamination
Problem Overview
Oil contamination can occur when oil from the compressor lubricates the air but doesn’t get filtered out effectively. This can be problematic for systems requiring clean, dry air.
Symptoms
- Oily residue on equipment and surfaces
- Frequent maintenance issues with air tools
- Reduced product quality in sensitive applications
Solution
Use coalescing filters designed to remove oil aerosols. Regularly inspect and replace these filters according to the manufacturer’s recommendations. Consider using oil-free compressors if oil contamination is a recurring issue, especially in industries like food processing and pharmaceuticals.
4. Ineffective Filtration
Problem Overview
Sometimes, a filter may not be effective at removing contaminants due to improper selection or aging. This can lead to an increase in particulate and moisture levels in the compressed air.
Symptoms
- Increased wear on pneumatic tools
- Deterioration of product quality
- Frequent breakdowns in equipment
Solution
Review your filter specifications to ensure they meet your application requirements. Upgrade to filters that offer better filtration ratings or combine multiple filter types to address different contaminants. Regular testing of air quality can also help determine if your filters are performing effectively.
5. Pressure Drops
Problem Overview
Pressure drops can occur when the filter is too restrictive or is nearing the end of its life. This can lead to inefficient system performance and increased energy costs.
Symptoms
- Noticeable decrease in pressure at tools
- Slower operation of pneumatic devices
- Warning lights or alarms on equipment
Solution
Check the differential pressure across the filter. If the pressure drop is significant, it may be time to replace the filter. Ensure that the filter is correctly sized for your system’s flow rate. If pressure drops persist, evaluate the overall system layout for potential restrictions, such as bends or excessive lengths in piping.
6. Incorrect Installation
Problem Overview
Filters that are not installed correctly can lead to numerous issues, including air leaks, poor filtration, and increased maintenance needs.
Symptoms
- Visible air leaks around the filter
- Unusual noises from the compressor
- Consistent drop in air quality
Solution
Ensure proper installation by following manufacturer guidelines. Use appropriate fittings and ensure that the flow direction indicated on the filter matches the system’s airflow. If you’re uncertain about the installation, consider consulting a professional to avoid future complications.
7. Filter Element Failure
Problem Overview
Filter elements can fail due to fatigue, manufacturing defects, or exposure to harsh operating conditions. A failed element can compromise the entire filtration system.
Symptoms
- Sudden loss of air quality
- Increase in contaminants downstream
- Unusual pressure fluctuations
Solution
Regularly inspect filter elements for signs of damage or wear. Establish a preventive maintenance schedule to replace filter elements before they fail. Keep spare elements on hand to minimize downtime in case of unexpected failures.
8. Costly Repairs and Maintenance
Problem Overview
When filters aren’t properly maintained, the resulting damage to equipment can lead to costly repairs and extended downtime.
Symptoms
- Frequent breakdowns of air-powered tools
- Increased repair costs
- Longer production times
Solution
Implement a robust maintenance plan that includes regular filter checks, replacements, and system inspections. Educate staff on the importance of maintaining clean air systems to minimize oversight and ensure everyone is on the same page regarding maintenance practices.
9. Noise Issues
Problem Overview
Some filters can create noise due to improper functioning or air turbulence within the system. Excessive noise can be a sign of underlying problems.
Symptoms
- Loud or unusual sounds from the compressor
- Increased vibration in the system
- Complaints from staff about noise levels
Solution
Identify the source of the noise by inspecting the filter and surrounding components. If the noise persists, consider installing sound-dampening equipment or relocating the compressor to a less noisy area. Ensure all connections are secure and check for any damaged parts.
Conclusion
Maintaining compressed air filters is essential for the efficient operation of pneumatic systems. By being aware of common problems and implementing proactive solutions, you can keep your system running smoothly and avoid costly repairs. Regular inspections, proper installation, and timely replacements are key strategies to ensure that your compressed air filters perform effectively in 2024 and beyond. read more blog..
FAQs
- How often should I inspect my compressed air filters?
- Regular inspections should be done monthly, but high-use environments may require more frequent checks.
- What are the signs of a failing filter?
- Look for reduced airflow, unusual noises, or a significant drop in air quality.
- Can I clean and reuse my compressed air filter?
- Some filters can be cleaned, but many are designed for single use. Check the manufacturer’s guidelines.
- How do I choose the right filter for my system?
- Assess the type of contaminants, required airflow, and specific industry standards to select the appropriate filter.
- What should I do if I notice water in my air lines?
- Inspect your moisture separators and filters, and consider adding a dryer to your system to prevent further issues.