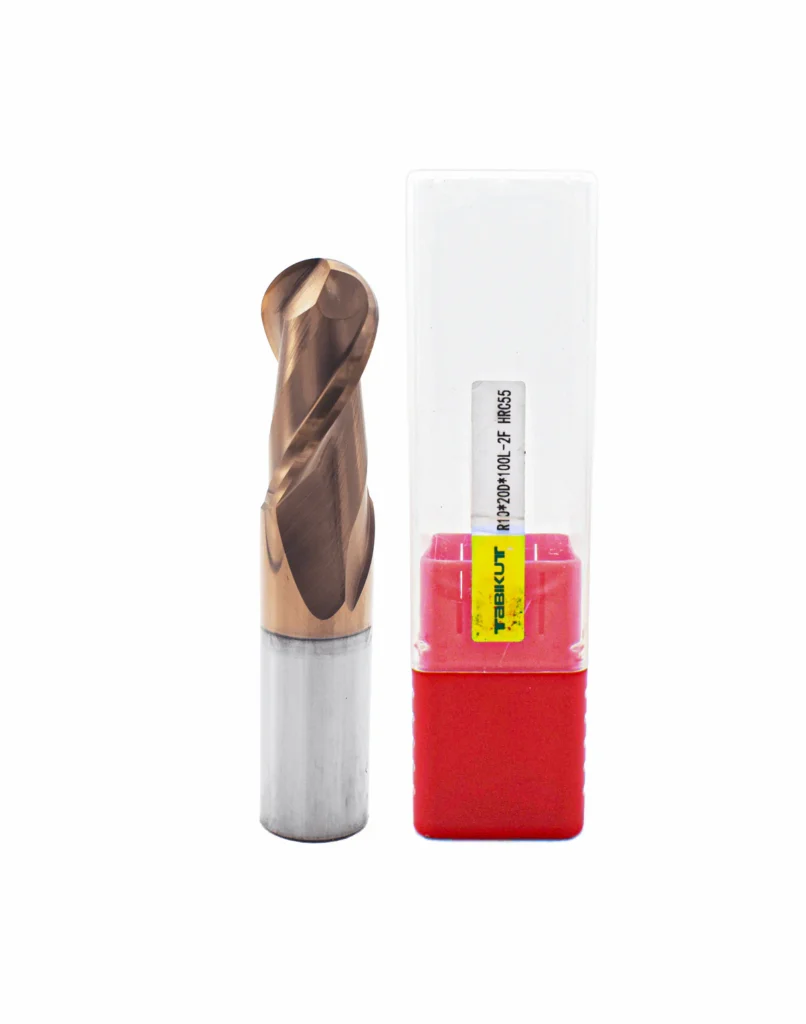
Precision and Durability in Cutting: Why Carbide Ball Nose Tools Are Industry Favorites
In modern machine machining, efficiency and precision are the most important factors. To meet these requirements, high-end cutting tools are always sought out by professionals. Of these tools, the carbide ball nose is widely used across industries due to its ability and accuracy.
What Is a Carbide Ball Nose?
A carbide ball nose is a kind of end mill distinguished by its round edge. This unique design allows for smoother contouring and intricate surface machining, which makes it an essential part of CNC tools. Made from tungsten carbide, these tools are renowned for their toughness and wear resistance, which means that they last longer as compared to conventional steel options.
Applications in Various Industries
The carbide ball nose is employed in a variety of industries. In aerospace engineering, complex 3D shapes and mold cavities can be made with these tools. Customized automotive prototypes as well as parts have also been efficiently shaped using carbide ball nose cutters. In the mold and die industry, their use has become a standard procedure because of the smooth surfaces they offer.
Complex parts that require high-dimensional precision are typically produced using carbide ball nose end mills. The intricate lines, curves, and fine detail are attainable easily, particularly when used in conjunction with high-speed CNC tools
Benefits Delivered by Carbide Ball Nose Tools
Many advantages are provided through carbide ball nose instruments:
- Extended Tool Life Because of the resistance to wear of the carbide tool, frequent replacements are not required.
- Superior Finish Quality Surface irregularities are minimized, and smooth surfaces are delivered consistently.
- Multi-dimensionality: Areas that are difficult to reach and narrow radii can be machined with no compromise on quality.
- The tool is resistant to heat The tool remains stable even under high-speed and high-temperature conditions.
As a result, it reduces downtime as well as operational efficiency, which increases across all manufacturing configurations.
What are the benefits of passive machining? Carbide Ball Nose Usage
In semi-automated or passive processing, stability and reliability are crucial. These characteristics are naturally supported by the carbide ball nose. When pre-programmed paths for tools follow CNC machines, constant efficiency is ensured. The shape of the tool permits uniform pressure distribution, which decreases the chance of breaking tools or uneven wear.
Maintenance and Best Practices
Even though carbide ball noses last a long time, certain maintenance procedures should be followed. Tools should be kept in dry conditions and inspected for cracks or chips prior to use. The best rates of feed and speeds must always be maintained and can be determined by the material being made.
Lubrication is frequently recommended to prolong the life of tools further and improve the removal of chips when cutting. When it is used in conjunction with cooling systems, more reliable results can be expected.
Trends in the Tooling Industry
A growing demand for high-precision, high-speed tools has been evident recently. In response, newer versions of carbide ball nose end mills have been designed with the latest coatings, such as TiAlN or AlCrN. These coatings improve the resistance to heat and also decrease friction, further improving the performance of the tool.
Furthermore, the trend towards the automation of manufacturing has resulted in increasing reliance on equipment which can produce results with minimal effort. In this regard, the ball nose made of carbide is still proving its worth.
Conclusion
The significance of the carbide ball nose in modern machining is not overstated. With its distinct design and long-lasting material composition, it has become the foundation of engineering precision. When it is employed in automotive, aerospace, or mold manufacturing, its advantages are always acknowledged. When this tool is integrated into everyday processes, significant improvements in finish quality, efficiency, and tool life can be made.